最適な倉庫レイアウトを実現する物流分析とは?
投稿日:2022.05.20 お役立ち情報
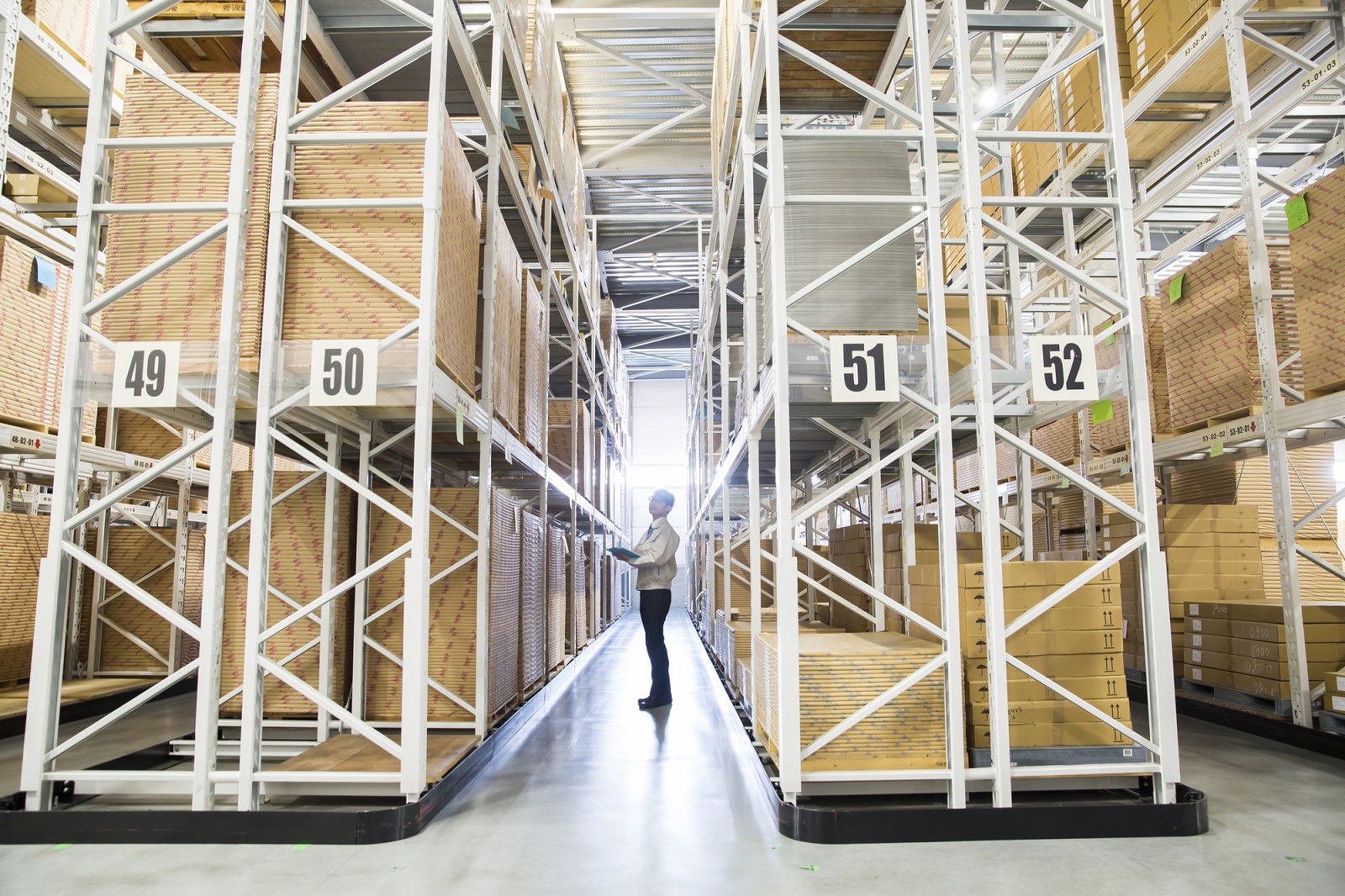
さらにここ数年の物流業界では、複数の拠点を1箇所の大規模物流センターに集約し、生産性向上や業務効率化を目指すという対策が行われるようになり、各倉庫で取り扱う商品数は莫大な数になっています。こういった状況から各倉庫では、倉庫内で取り扱っている莫大な数の商品を、いかに効率よく管理していけるのかが非常に重要な課題です。と言うのも、近年では、ネット通販などで個人向けに発送される機会が急増していることから、如何に低コストで効率的な管理ができているかが、物流企業の経営状況を大きく左右するようになっているからです。
そこでこの記事では、「いかに多くの商品を効率的に管理するのか?」と言う問題を解決するための一つの方法となる『物流分析(ABC分析)』について解説していきます。適切な物流分析ができれば、より生産性が高い倉庫レイアウトを実現することができると言われていますので、ぜひ参考にしてみてください。
Contents
最適な倉庫レイアウトにするメリットとは?
物流業界を取り巻く環境が急速に変化している中、「最適な倉庫レイアウトを作るにはどうすれば良いのか?」と言う問題に悩まされている事業者様も多いと思います。そもそも、倉庫レイアウトを改善するということは、大掛かりな作業が必要で、コストもかなり掛かるという問題から、そう簡単に手を出すことができない問題でもあるでしょう。しかし最適化された倉庫レイアウトは、それらの問題点を上回るメリットも存在しています。
メリット1 コスト削減
倉庫レイアウトの最適化は、最終的にコストの削減ができるというメリットが得られます。例えば、適切な物流分析を行い、出荷頻度の高い商品をピッキングしやすい場所にまとめることが出来れば、無駄な動きを省きスムーズに作業が進むようになりますので、それだけ人件費の削減が期待できます。また、デッドスペースを上手に削減できれば、現在の施設で保管量を増やすことができ、倉庫の拡充を避けたり、遅らせたりすることができます。これだけで非常に大きなコスト削減効果が得られると分かります。
倉庫レイアウトの最適化は、今ある倉庫スペースを最大限有効活用することにつながりますので、余計なコストを削減し、なおかつ作業効率まで向上できる、ベストな倉庫の姿を作り出せます。
メリット2 人的ミスや事故の予防
近年では、自動化やロボット化により人的ミスの削減を目指すという対策が有名です。ただ、最適な倉庫レイアウトに改善するだけでも、人的ミスや事故を予防することができます。
そもそも、倉庫での人的ミスは、業務や作業動線、在庫数に倉庫レイアウトが見合っていないなどと言う問題から、ピッキングの際に間違った商品をとってしまうといったことが原因で発生します。さらに、無計画に商品が置かれているレイアウトの場合、倉庫内の見通しが悪くなり、従業員同士が衝突してしまうなどの事故を生むリスクも高くなります。
最適な倉庫レイアウトに改善できれば、従業員が安全にスムーズに作業できるようになり、倉庫作業に潜むさまざまな問題を予防してくれるようになります。
このように、最適な倉庫レイアウトに改善することができれば、さまざまなメリットを得ることができます。それでは、自社にとって最適な倉庫レイアウトがどのようなものなのかを判断するにはどうすれば良いのでしょうか?実は、きちんと物流分析を行うことで、自ずと最適な倉庫レイアウトが見えてくると言われています。以下で、EC市場の拡大が続く中、物流業界で注目されている『ABC分析』がどういったものなのかを簡単に解説しておきます。
物流の分析方法について
それではここからは、最適な倉庫レイアウトを実現するために、非常に重要な要素となる物流分析について解説していきます。倉庫は、「商品を一時的に保管しておくための場所」ですので、取り扱う商品の種類やそれぞれの在庫数をきちんと把握しておかなければいけません。もし、一人で把握可能な商品点数を保管する倉庫であれば、どこの棚に何があるのかは台帳などをつけていれば把握することが可能です。しかし、取り扱う商品数が増えていくと、個人ではとても把握できませんので、何らかの方法で効率的に管理しなければいけません。特に、EC市場が拡大を続ける近年では、倉庫内に数万点以上にのぼる種類の商品を保管するケースも考えられ、適当に棚に収納してしまうと、どこに何を置いたのかがわからなくなり、現場が混乱してしまうことになります。
そこで現在では、多種多様な商品を保管する倉庫では、それぞれの商品を同様に管理するのではなく、優先度を決めて管理する方が、コスト的にも効率的にも最適な管理方法だと考えられるようになっています。そして、保管する商品の優先度を決定する手法として物流管理現場で注目されているのが『ABC分析』と呼ばれる手法になります。
ABC分析とは
ABC分析は、売り上げなどに関するデータを把握するための基本的な分析法で、『重点分析』などとも呼ばれます。
従来の倉庫の在庫管理では、用途別に商品を分けて管理するという方法がありました。例えば、建材であれば『屋根材』『外壁材』『床材』『内装』と言うような分類方法です。管理の面から見れば、非常に単純で分かりやすいように思えますが、EC市場が拡大した現在では、物流倉庫で取り扱う商品の種類が莫大な数になるということを忘れてはいけません。さらに、保管する商品が全て平均的に同数ずつ売れるようなことはありませんし、商品の販売価格もさまざまです。つまり、全ての商品を同列に扱って管理していくという方法は、非効率だと考えられています。
ABC分析は、それぞれの商品の売上高(販売金額)に着目する分析方法で、売上高が高い商品ほど『優先度が高い商品』とみなします。要は、受注が期待できる人気の高い商品は重点的に在庫管理や品質管理を行いますが、ほとんど売れない商品群には人件費などのコストをあまりかけないようにするという手段になります。
実際にABC分析を倉庫に導入する場合は、各商品を売上高が大きい順にA、B、Cと並べて、分類・管理します。具体的には、企業の売り上げの70%に含まれる商品群をAグループとし、70~90%に含まれる商品群がBグループ、そしてそれ以外がCグループといった分類を行います。Aグループの商品群は、自社の売上高70%を占める売れ筋商品となる事から、当然在庫管理や品質管理も入念に行い、欠品などで機会損失が出ないように細心の注意を払います。その一方、最も売り上げに貢献しないCグループに分類される商品に関しては、在庫を削減するための対象になります。つまり、こういった売上への貢献度をもとに、重要度の高い商品とそうでない商品をグループ分けすることで、より効率的な管理が行えるようになるわけです。
ABC分析は、利益率向上や作業の効率化によって企業の経営力を高めることが目的とされています。売れ筋であるAグループの商品を、欠品などが出ないように適切に管理しておけば、それだけ機会損失のリスクを低減することが可能です。一方、売り上げに貢献しないCグループの商品については、保管場所を縮小して在庫数を減らすことで、無駄な在庫リスクを低減することが可能です。
物流分析を行うメリット
それでは最後に、物流倉庫などが適切に物流分析を行っていくことのメリットについても簡単に解説しておきましょう。
多種多様な商品を保管する物流倉庫などで適切な物流分析を行うことは、倉庫の現状を可視化することができる点が大きなメリットです。例えば、上述したABC分析を行い、売れ筋の商品や高利益を生み出す商品を可視化することができれば、どの商品に注力すれば良いのかが明確になります。さらに、現状の倉庫内での保管場所や方法、ピッキング動線が本当に正しいのかが可視化でき、より効率的な倉庫レイアウトが自ずと見えてくるという非常に大きなメリットがあります。
物流業務で考えると、Aグループの売れ筋商品は、ピッキング動線が最短になるように保管配置を見直すことで、生産性向上を見込むことができるでしょう。さらに、出荷頻度が最も低いCグループの商品などについては、作業効率よりもスペース効率を優先し、背の高い棚やスチールラックの上部に保管するようにして、出荷頻度の高い商品の在庫量を増やすといった工夫ができるようになるでしょう。
このような分析を定期的に行うことで、顧客のニーズまで反映した「今の時代に最も適切な倉庫レイアウト」を常に作ることができるようになる点が物流分析を行うメリットです。
まとめ
今回は、最適な倉庫レイアウトを実現するため、非常に重要な要素となると言われる物流分析について解説してきました。倉庫は、「物品を一時的に保管しておく場所」であることは間違いありませんが、保管している物品は「いずれ出荷されることになる」と言う点を忘れてはいけません。
何も考えずに「スペースがあいているから」と言う理由で保管場所を決めていけば、本来出荷頻度が高い商品なのに他の商品に隠れてしまい、ピッキングの作業効率を低下させてしまうといった問題を引き起こすリスクがあります。逆に言えば、きちんと物流分析を行い、その結果をもとに倉庫レイアウトを作っていけば、最も作業効率が良い配置で保管できるようになるため、今まで無駄が発生していた人件費なども削減することができるようになります。
倉庫は、「物品を保管する場所」ですので、保管量ばかりにこだわってしまうケースがありますが、「保管したものは出荷する」と言うことも忘れないようにしましょう。
関連記事
ARCHIVE
TAG
- #食品物流センター
- #動画開設
- #配棟計画
- #パレット共通化
- #レンタルパレット
- #大阪万博
- #建築費動向
- #トラックGメン
- #ブラック荷主
- #物流クライシス
- #建設準備
- #グラフ
- #建築費
- #ドライバー不足
- #立地
- #2024年問題
- #3PL
- #3温度帯
- #4温度帯
- #AGV
- #AI
- #AVG
- #CAS冷凍
- #EC
- #FSSC22000
- #GDPガイドライン
- #IoT
- #IT
- #LED
- #RiSOKOセミナー
- #Society 5.0
- #Third Party Logistics
- #エアコン
- #カーボンニュートラル
- #ガソリン
- #グッズ
- #コールドチェーン
- #コロナ
- #コロナ禍
- #システム建築
- #タグを削除: RiSOKOセミナー RiSOKOセミナー
- #デバンニング
- #トラック待機時間
- #バンニング
- #ひさし
- #ピッキング
- #フォークリフト
- #プラスチック削減
- #フルフィルメント
- #プロトン凍結
- #フロン排出抑制法
- #フロン管理義務
- #マテハン
- #マテハン機器
- #メディカル物流
- #ラック
- #リチウムイオン蓄電池
- #ロボット
- #ロボット化
- #中小企業支援策
- #事故事例
- #人手不足
- #人材不足
- #低温倉庫
- #低温物流
- #保安距離
- #保有空地
- #保管効率
- #保管場所
- #保管温度帯
- #倉庫
- #倉庫の強度
- #倉庫の種類
- #倉庫建設
- #倉庫建設コンサルタント
- #倉庫新築
- #倉庫業法
- #倉庫火災
- #免震
- #共同物流
- #冷凍倉庫
- #冷凍自動倉庫
- #冷凍食品
- #冷蔵倉庫
- #冷蔵庫
- #削減
- #労働時間
- #労働災害
- #医療機器
- #医療物流
- #医薬品
- #医薬品の物流業務
- #医薬品保管
- #医薬品倉庫
- #危険物
- #危険物倉庫
- #危険物施設
- #営業倉庫
- #国際規格
- #土地
- #地震
- #地震対策
- #基礎知識
- #安全
- #安全対策
- #定期点検
- #定義
- #対策
- #屋内タンク貯蔵所
- #屋内貯蔵所
- #工場
- #工場の衛生管理
- #建築基準法施行令
- #建設計画
- #従業員
- #感染予防
- #技術
- #換気設備
- #改修工事
- #政令
- #新型コロナウイルス
- #新築
- #施設設備基準
- #機能倉庫建設
- #水害
- #水害対策
- #治験薬
- #法律
- #消防法
- #消防設備
- #温度管理
- #火災
- #火災対策
- #災害
- #無人搬送ロボット
- #無人搬送車
- #無人配送車
- #燃料費
- #物流
- #物流DX
- #物流センター
- #物流倉庫
- #物流倉庫新設
- #物流倉庫自動化
- #物流拠点
- #物流業界
- #物流総合効率化法
- #物流課題
- #特殊倉庫
- #用途地域
- #異物混入
- #着工床面積
- #空調
- #結露
- #耐震工事
- #職場認証制度
- #自動倉庫
- #自動化
- #自動車運送事業者
- #衛生管理
- #補助金
- #規制緩和
- #調理器具
- #貸倉庫
- #軽油
- #適正流通ガイドライン
- #関西物流展
- #防災
- #防災用品
- #防爆構造
- #集中豪雨
- #電気代
- #電気代削減方法
- #静電気
- #静電気対策
- #非危険物
- #非接触
- #食品倉庫
- #食品物流
- #食品衛生法
もっと見る▼